Biodiesel Transesterification

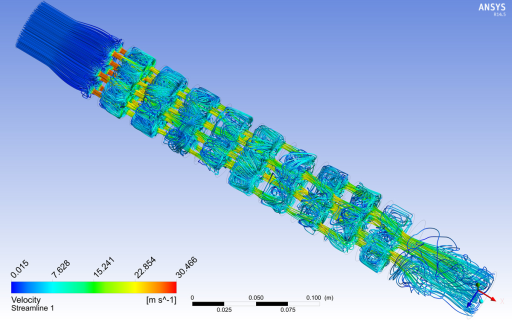
Capacity 100 T/D to 1000 T/D
Process Highlights
- Multipurpose and fully automatic continuous process
- High product yield
- High quality biodiesel and glycerin
- Clear phase separation
Advantages
- Suitable for various raw materials
- Based on catalyzed transesterification
- Direct conversion with no intermediate steps
- Minimal side reactions and reaction time
- Low catalyst consumption
Customer Benifits
- High flexibility
- Handling of various feed stock
- Reduction of operating and maintenance cost
- Fast ROI
In heterogeneous liquid–liquid reactions, cavitational collapse at or near the interface will cause disruption and mixing, resulting in the formation of very fine emulsions. When such emulsions are formed, the surface area available for the reaction between the two phases is significantly increased, thus increasing the rates of reaction. This is beneficial, particularly in the case of phase transfer-catalysed reactions or biphasic systems. A major competitive advantage is our patented multistage cavitation reactors which we use for transesterfication process in production of biodiesel.
The different ways in which cavitation can be used beneficially in the biodiesel processing applications are:
|
|
Multiple Feedstocks. Our systems are designed to use various feedstocks such as palm oil, yellow grease, and tallow simultaneously which allows them to combine and use the lowest cost available feedstock. This also allows clients to shift into and out of different feedstocks based on customer demand and market cost dynamics without hindering their production process or substantially increasing operating costs.
Our Biodiesel Production Process
With our patented multi-stage cavitation process we have optimized our biodiesel production process to incorporate new, internally developed, proprietary technology. Compared to conventional methods of biodiesel production, our process offers superior quality biodiesel while minimizing the amount of harsh chemicals used, offering a major competitive advantage to our customers.
Biodiesel is produced in a relatively simple process known as transesterfication. Typically in this process, vegetable oil or animal fat feedstock is chemically reacted with an alcohol, such as methanol or ethanol, and a catalyst, such as sodium or potassium hydroxide. In our cavitation-based NANO reactor technology, this transesterification process is carried out at molecular level through an intensive cavitation process. All components, including vegetable oil or animal fat feedstock, alcohol and catalyst, are subjected to high pressure impulses and advanced controlled nano-technology cavitation. In heterogeneous liquid–liquid reactions, cavitational collapse at or near the interface causes disruption and mixing, resulting in the formation of very fine emulsions. When such emulsions are formed, the surface area available for the reaction between the two phases is significantly increased, thus increasing the rates of reaction. This intensive cavitation process in the NANO reactor systems (hydrodynamic cavitator) creates micro-explosions which leads to the breakdown of fatty acid molecules and results the production of superior quality biodiesel.
Our NANO reactor systems are designed to use various vegetable oils and feedstocks such as palm oil, yellow grease, and tallow simultaneously. This enables producers to utilize different feedstocks based on customer demand and market cost dynamics without hindering their production process or substantially increasing operating costs. Our reactors can be operated on a continuous basis, integrated into existing facilities and production plants, and can be designed for various capacities ranging from 100 TPD to approximately 1000 TPD.
Refining feedstock in the blink of an eye
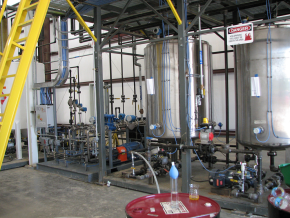
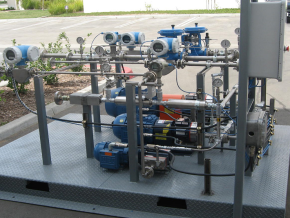
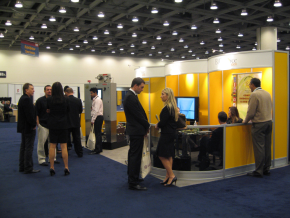
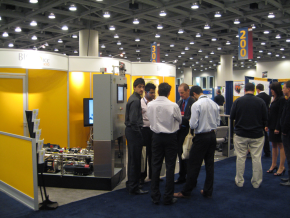
* Click on the image to see a full-size version